Mounted flap wheels
Mounted Flap Wheel, 2-1/2" x 1-1/2, 40 Grit, 1/4" Shank, Ceramic oxide CO-COOL
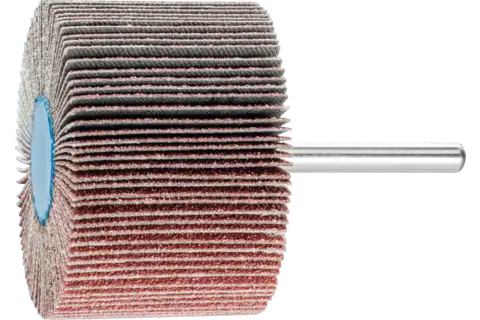
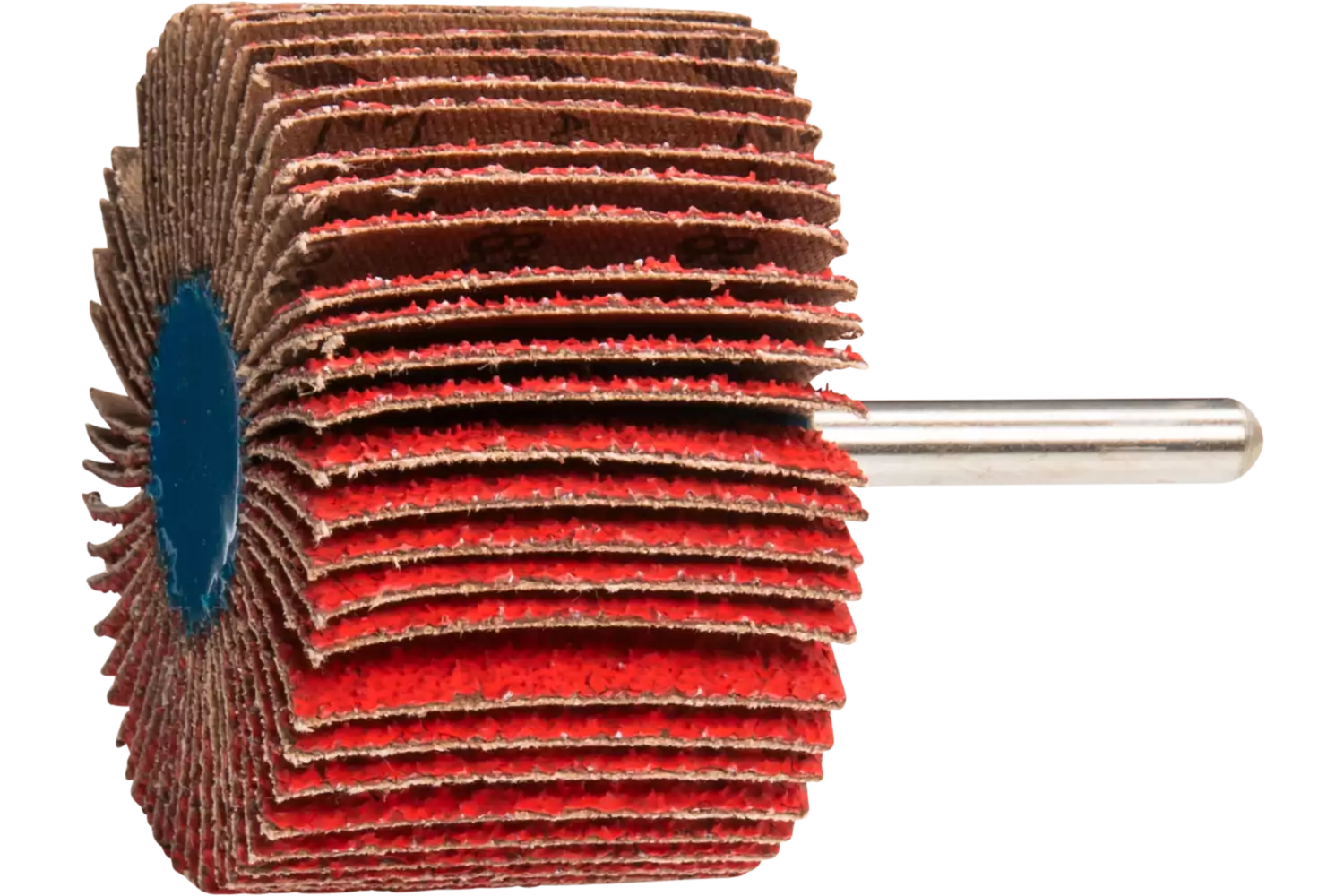
Technical information
Mounted Flap Wheel, 2-1/2" x 1-1/2, 40 Grit, 1/4" Shank, Ceramic oxide CO-COOL
- Item number Global part number
- 47800160
- Abrasive
- CO-COOL
- Dia. external
- 2 1/2 Inch
- Dia. shank
- 1/4 Inch
- EDP number
- 45443
- Grit size
- 40
- Length, shank
- 1 1/2 Inch
- Max. RPM
- 13000 RPM
- RPM, optimum
- 6300 RPM
- Width
- 1 1/2 Inch
- Packaging unit
- 10 pieces
Description
Advantages
Recommendations for use
Safety notes
- Workpiece materials
- Applications
- Compatible power tools
PFERDVALUE