Our tips for industry on how to maximize the tool life
A key priority for anyone who uses tools is extending the tool life, as it plays a crucial role in cutting operating costs and sharpening your competitive edge. This article discusses some of the things to bear in mind in order to optimize the tool life, and provides practical tips to help you on your way.
What does “tool life” mean?
The tool life is a key parameter for tools that are designed to remove material from a workpiece. The term denotes for how long you can use a tool without problems before it begins to show major signs of wear. At this point, some tools then need to be serviced or even replaced entirely. The tool life only looks at the time in which the tool is actually performing productive work.
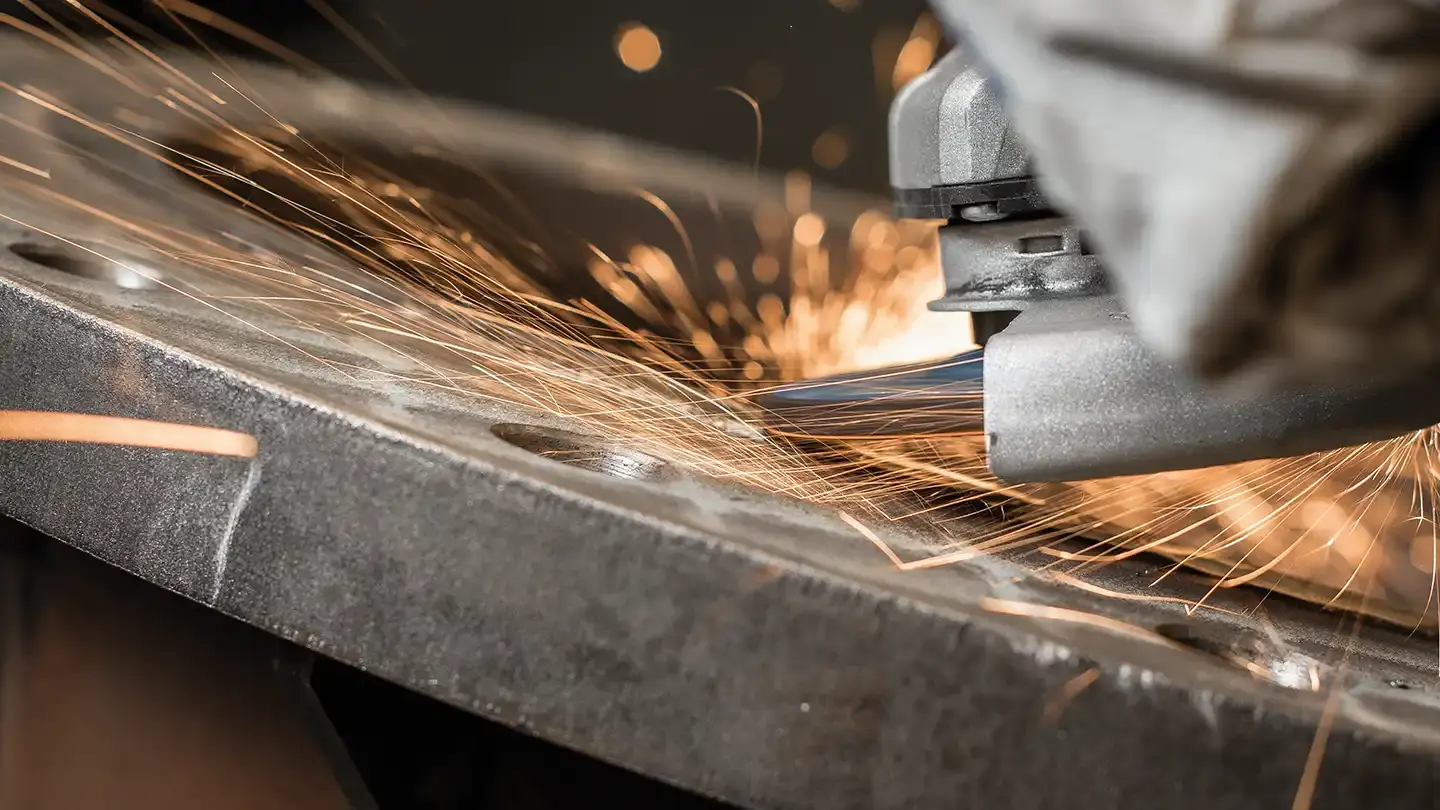
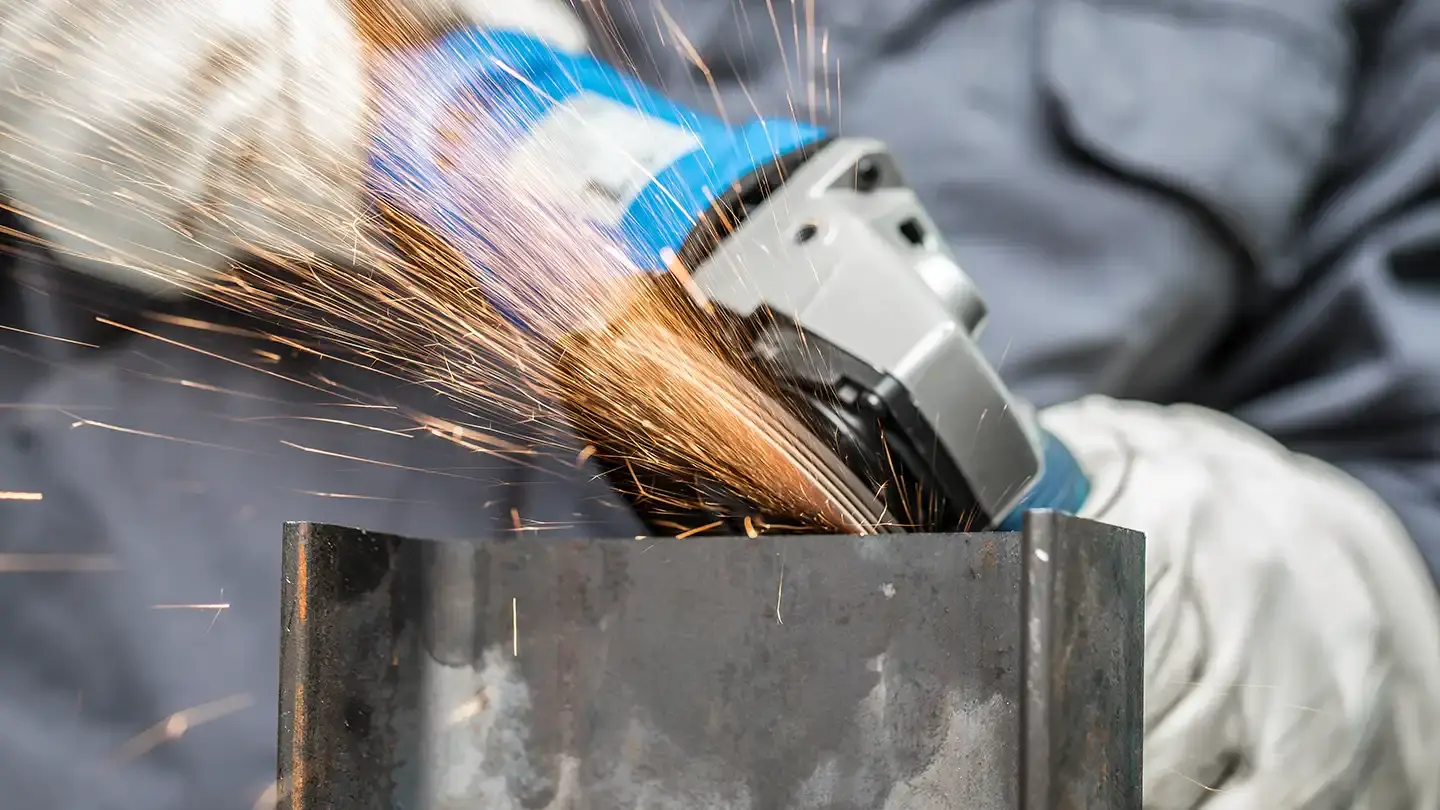
Why is the tool life so important?
Tools that have reached the end of their tool life will have signs of wear that negatively affect how they work and how precise they are. This means you need to replace them and are left facing non-productive time as you set up the tools again.
In addition, if you use a worn tool to machine surfaces, you run the risk of causing deviations such as unevenness or differing dimensions, which then causes more rejects. In a nutshell, a longer tool life is directly associated with lower operating costs and higher-quality products.
Which factors influence the tool life?
Continuous machining work places the tool under stress, either from the mechanical load or due to changes in temperature whilst the tool is being used. Tool life is not an isolated phenomenon, and the following parameters have a significant impact on how long a tool lasts:
- The specific tool geometry, which defines its shape and structure.
- The raw material used to manufacture the tool, which plays a major role in determining its durability and performance.
- The stock removal conditions, including the cutting speed and cutting depth.
- The condition of the workpiece being machined.
- The temperature of the tool and workpiece and any changes during the production process.
- The drive system being used.
- How experienced and competent the user is.
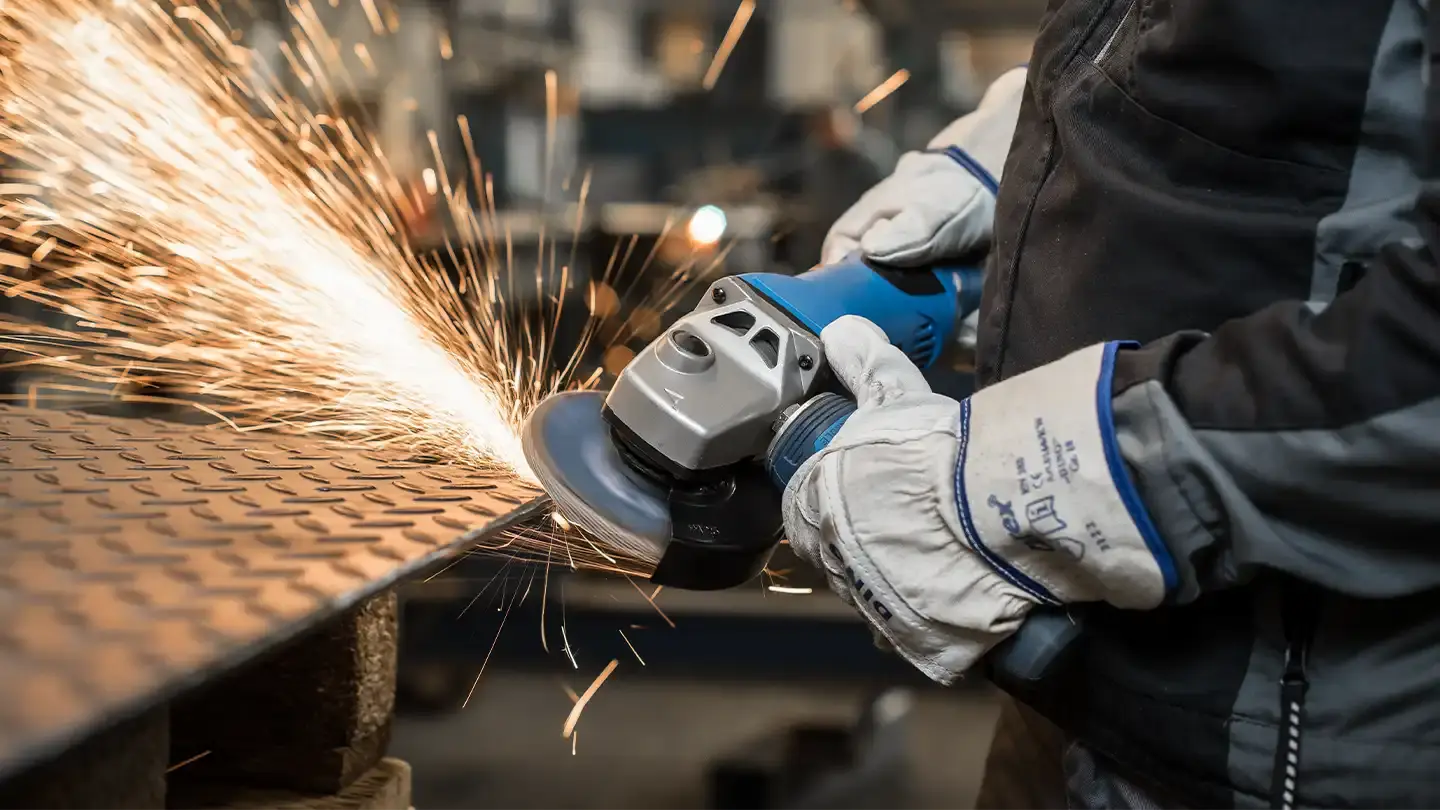
Tips for extending the tool life
Below are some recommendations for optimizing the tool life and maximizing efficiency and profitability:
- Cutting speed: It is crucial to set the cutting speed precisely. If the cutting speed is set too high it can cause the tool to overheat, which can make it wear down faster. However, it must not be set too low either as this will mean the abrasive grain will not work correctly. Carefully adjusting the cutting speed will enable you to maximize the tool life and boost your productivity.
- Cutting depth: Choosing a suitable cutting depth can reduce the number of cuts required to produce the desired result, which is good for the tool life.
- High-performance tools: Choosing the right tool for the task at hand can yield great benefits. High-performance tools are generally more resistant to wear, meaning they can significantly extend the tool life.
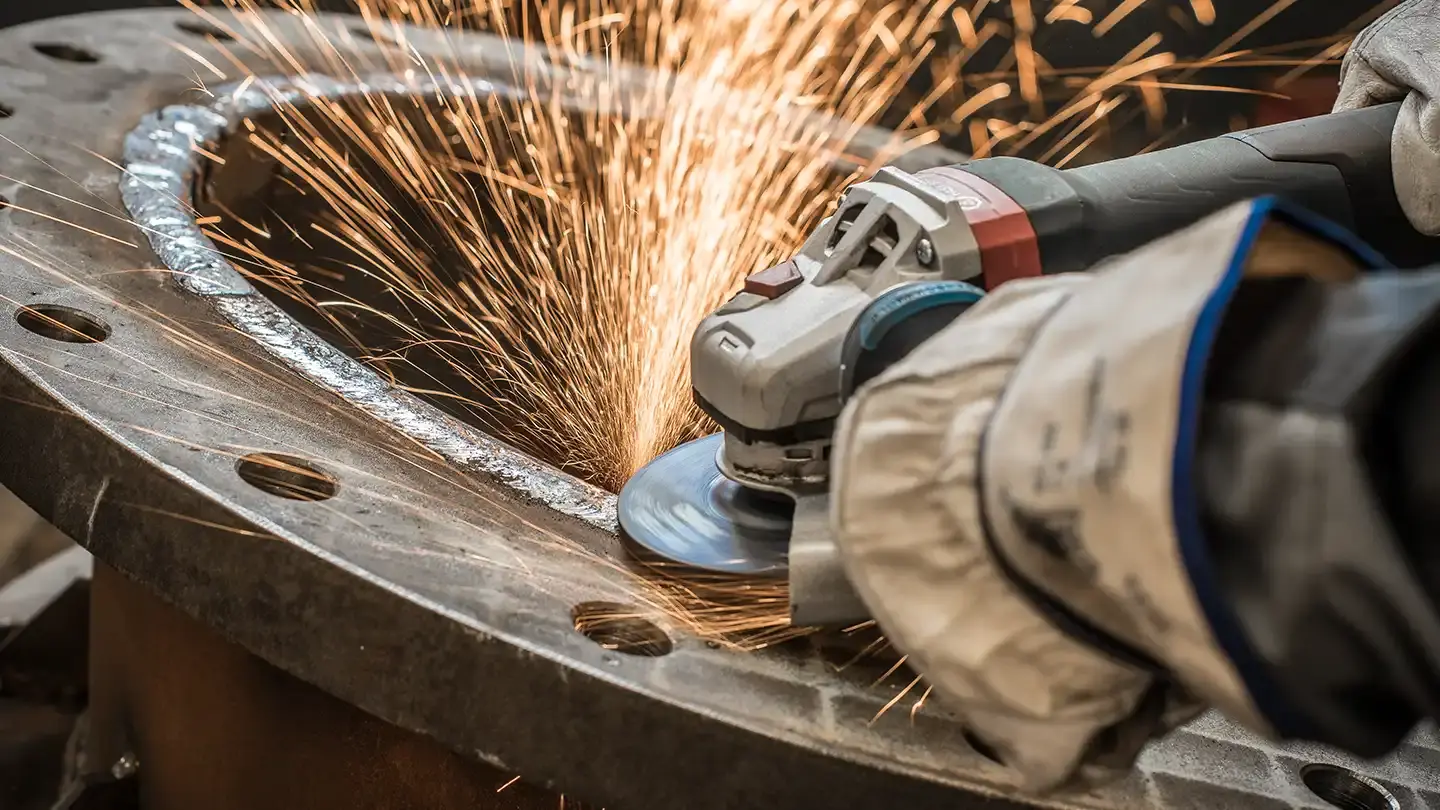
As these recommendations show, by choosing the right tool and using it in the right way you not only improve product quality, you also pave the way for major cost savings. Naturally, the same applies to coated abrasives, too. We’d be pleased to provide a no-obligation consultation, working hand in hand with you to determine which parameters you should focus on for your specific processes.
Outstanding tool life and the first choice for steel
the POLIFAN Z 40 SG POWER STEELOX flap disc from PFERD TOOLS
When it comes to high-performance tools, the powerful POLIFAN Z 40 SG POWER STEELOX flap disc from PFERD TOOLS provides an unparalleled tool life.
The upgraded Z 40 grit increases the overall stock removal rate by up to 75% and extends the tool life – all whilst offering maximum aggressiveness over the entire tool life.
You can easily level up to 30 metres of weld seam per flap disc. All this makes the POLIFAN Z 40 SG POWER STEELOX the most economical solution – and the first choice for the steel processing industry.
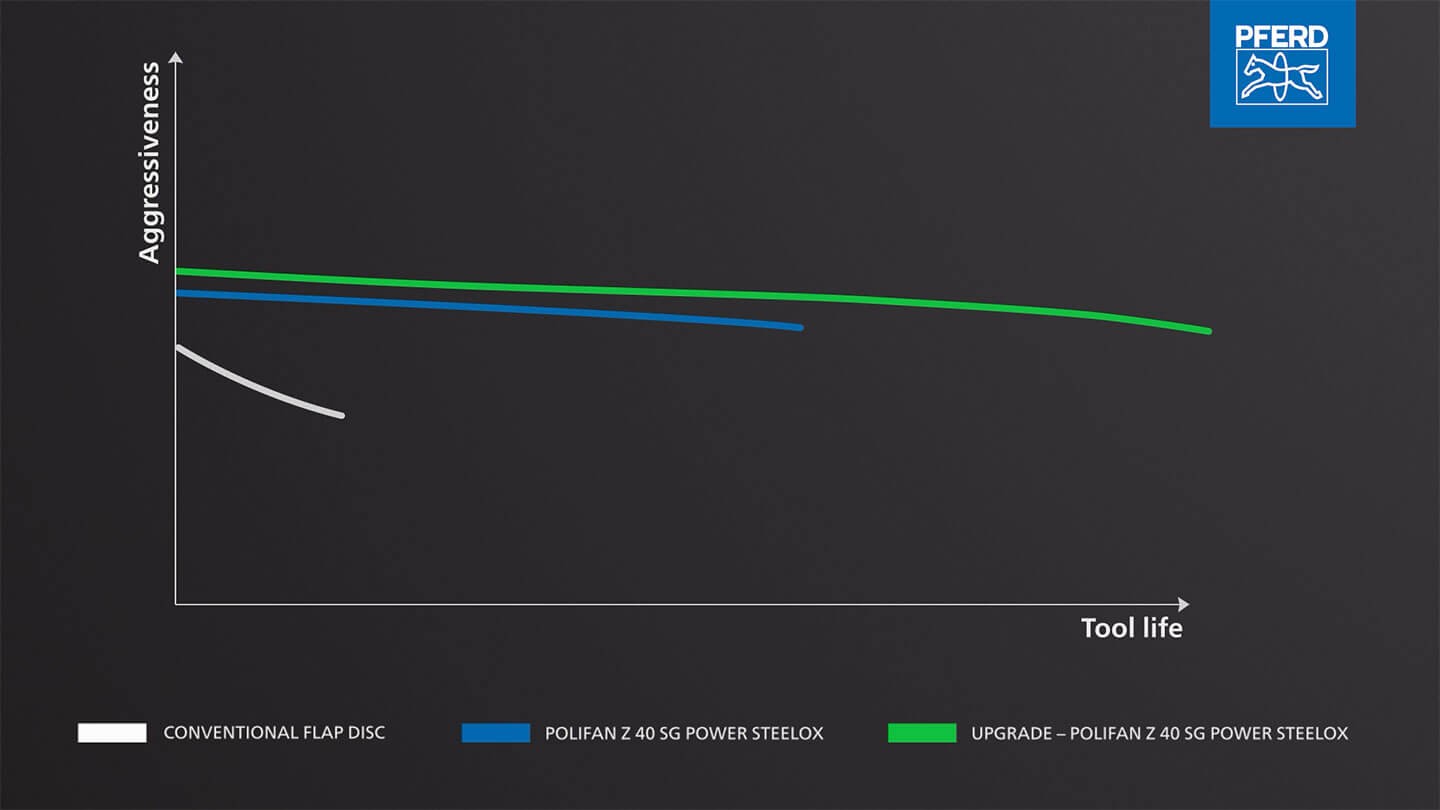