Working on edges using tungsten carbide burrs
Why is working on edges so important?
Working on edges removes any protrusions on the workpiece, thereby minimizing the risk of injury.
In numerous industries, working on edges also has paramount importance. Defined edges are a requirement for the correct welding of components (V-shaped welds). They also have a crucial impact on the durability of components.
When iron and steel oxidize in the presence of water (e.g. in the atmosphere, in water and in the ground), this can result in corrosion and the formation of rust. Corrosion (rust) presents a great problem when it comes to using and processing steel. Rust is not only unsightly, but it also weakens the material.
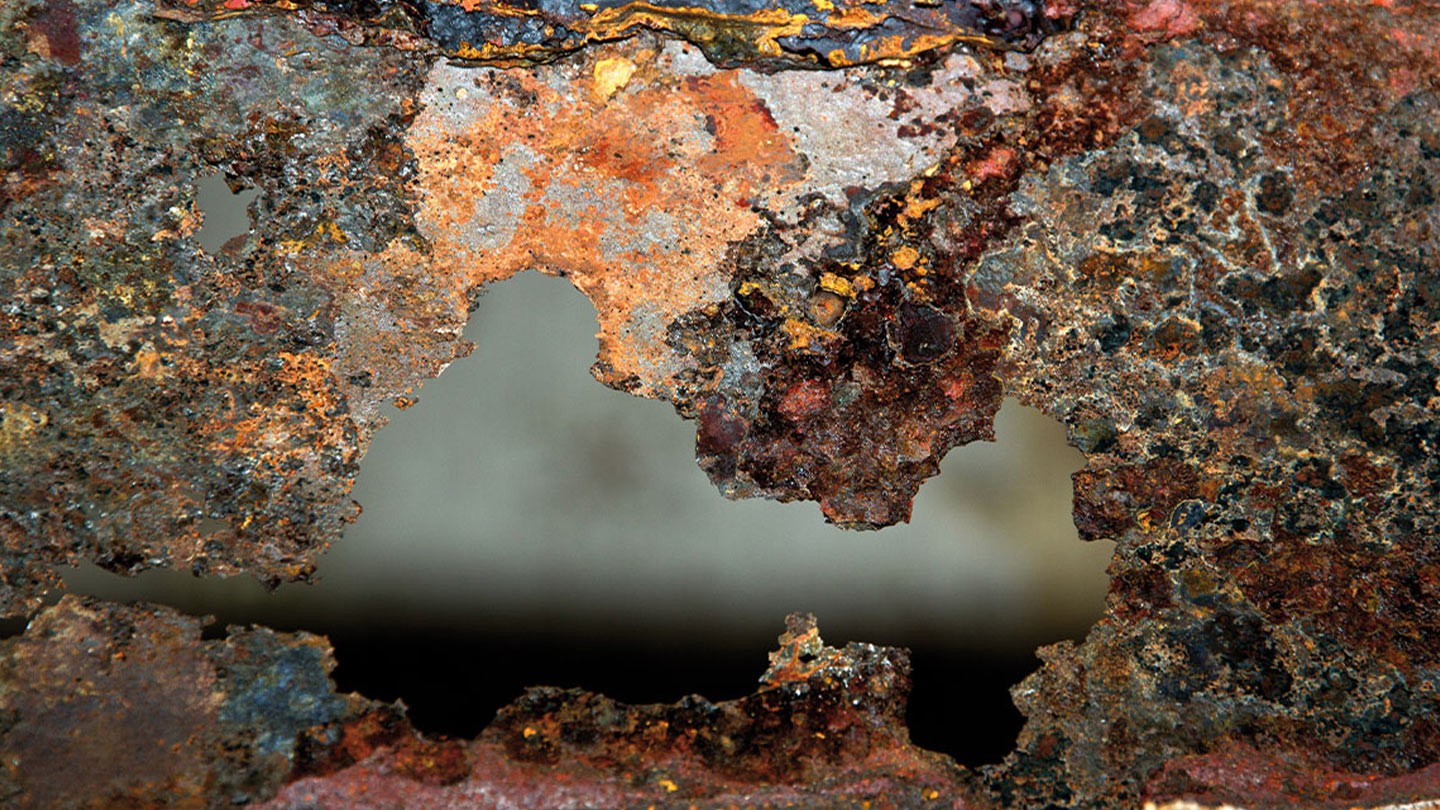
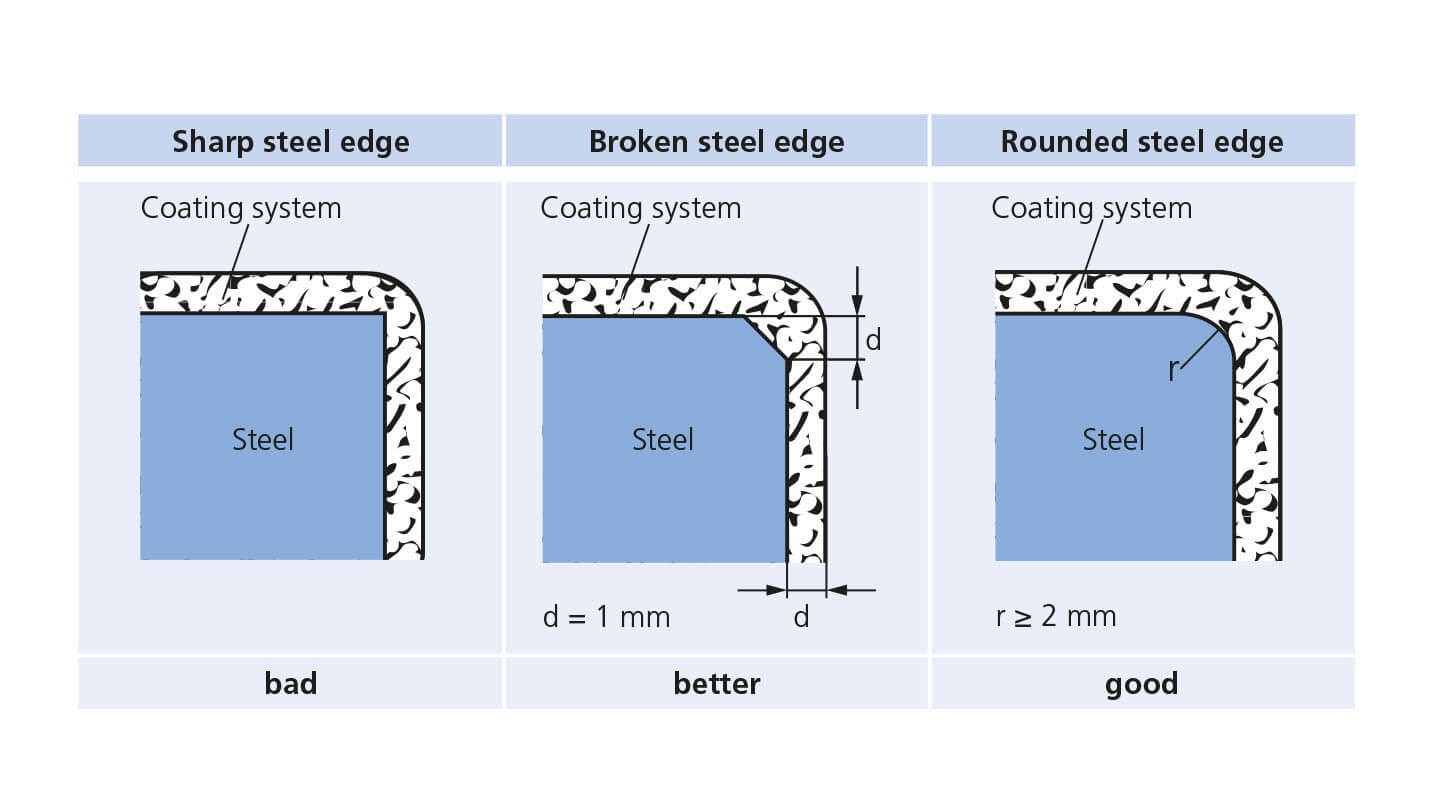
To protect workpieces against corrosion (rust), coating systems such as paint, powder coatings or metallic coatings are often used. The quality of the surface to be coated has a crucial impact on the quality of the corrosion protection measures.
Coatings on sharp edges have a thinner layer than on flat surfaces. The protective layers flake off more frequently and also damage more easily.
In contrast, rounded edges ensure that the coating is applied evenly with a sufficient thickness. All of the sharp edges on a component must therefore be deburred, blunted, and ideally rounded to a radius of ≥ 2mm.
PFERD TOOLS recommends tungsten carbide burrs with the EDGE cut for the defined rounding of edges as part of the perfect preparation for coating processes
In addition to working on edges as a safety or corrosion protection measure, rounded edges also play an important role from an aesthetic point of view.
What types of work on edges are there?
We can distinguish between two types of application when it comes to working on edges:
- Defined work on edges
- Flexible work on edges
PFERD TOOLS offers cuts and versions for both flexible as well as for defined work on edges.
What burr forms are suitable for defined work on edges?
The following burr forms are available for defined work on edges:
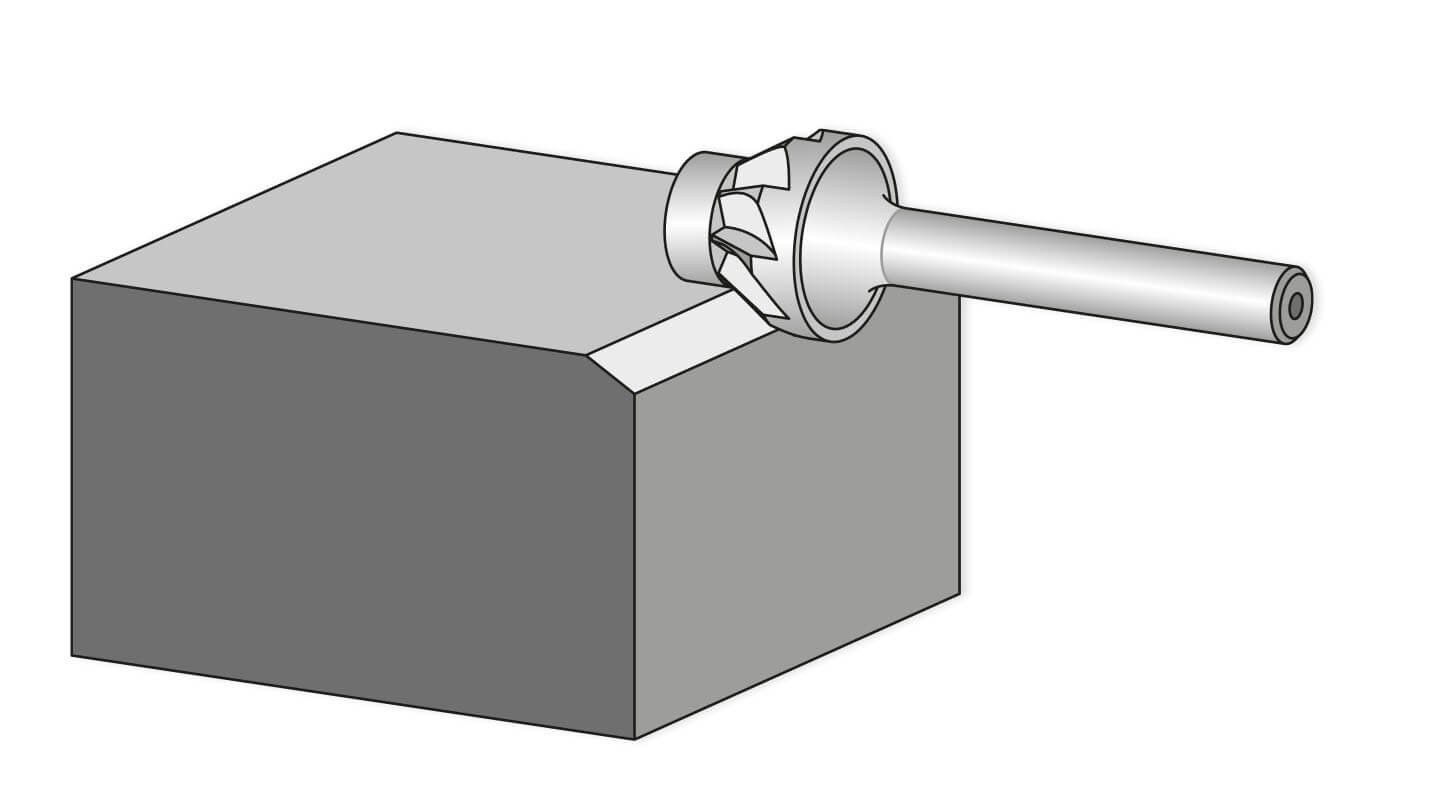
Conical counterbore shape EDGE
Conical counterbore burrs with the designation EDGE create precisely defined chamfers. Depending on the version, you can create chamfer angles of 30° or 45°.
Burrs with a chamfer angle of 45° can be used in conjunction with the EDGE Cutting System. The width of the chamfer created is 1.2 mm (+/- 0.2 mm).
Concave radius burrs V EDGE
Concave radius burrs with the designation EDGE create precise radii. They are suitable for creating and processing 3mm outer radii and can be used in conjunction with the EDGE Cutting System. The burrs cannot be resharpened.
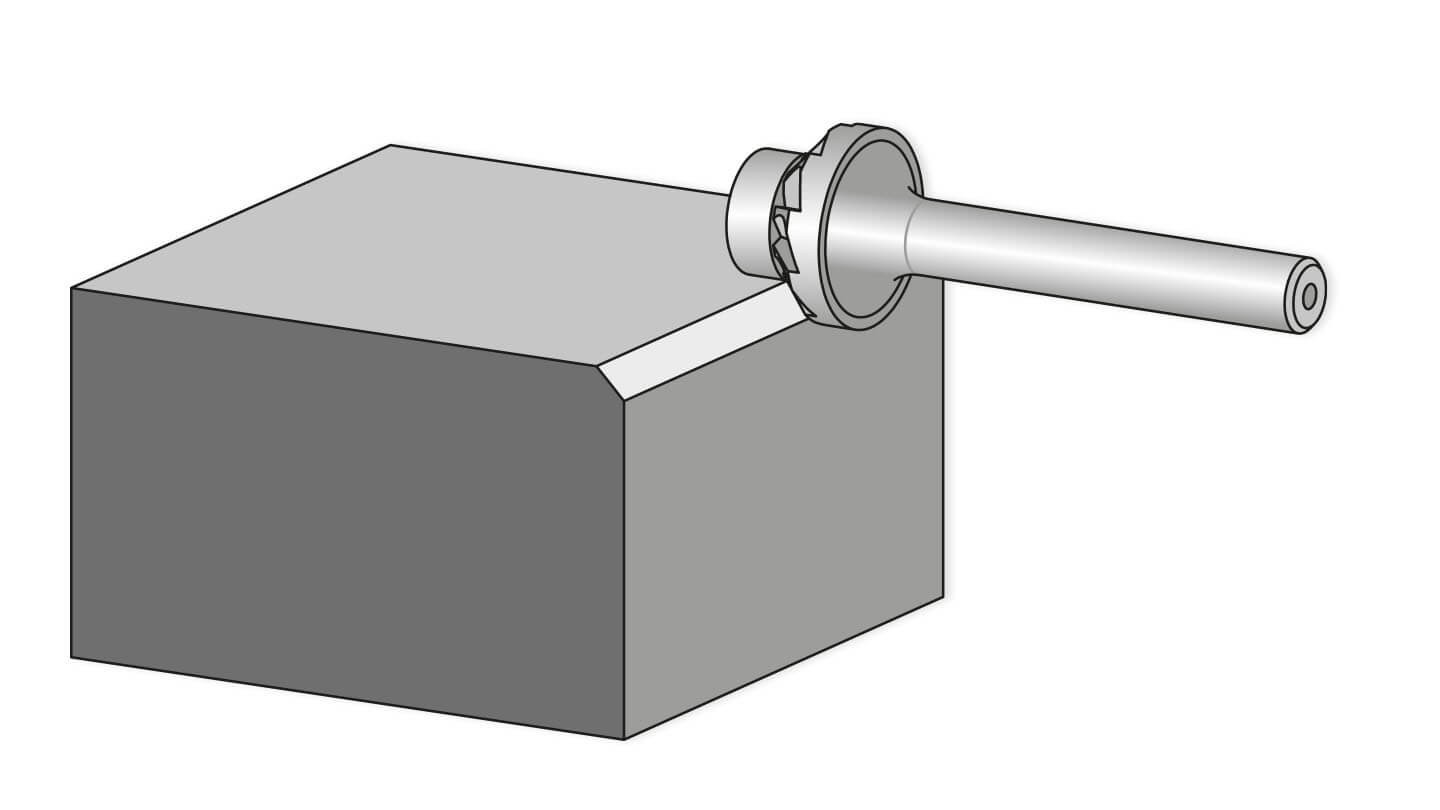
What cut is suitable for defined work on edges?
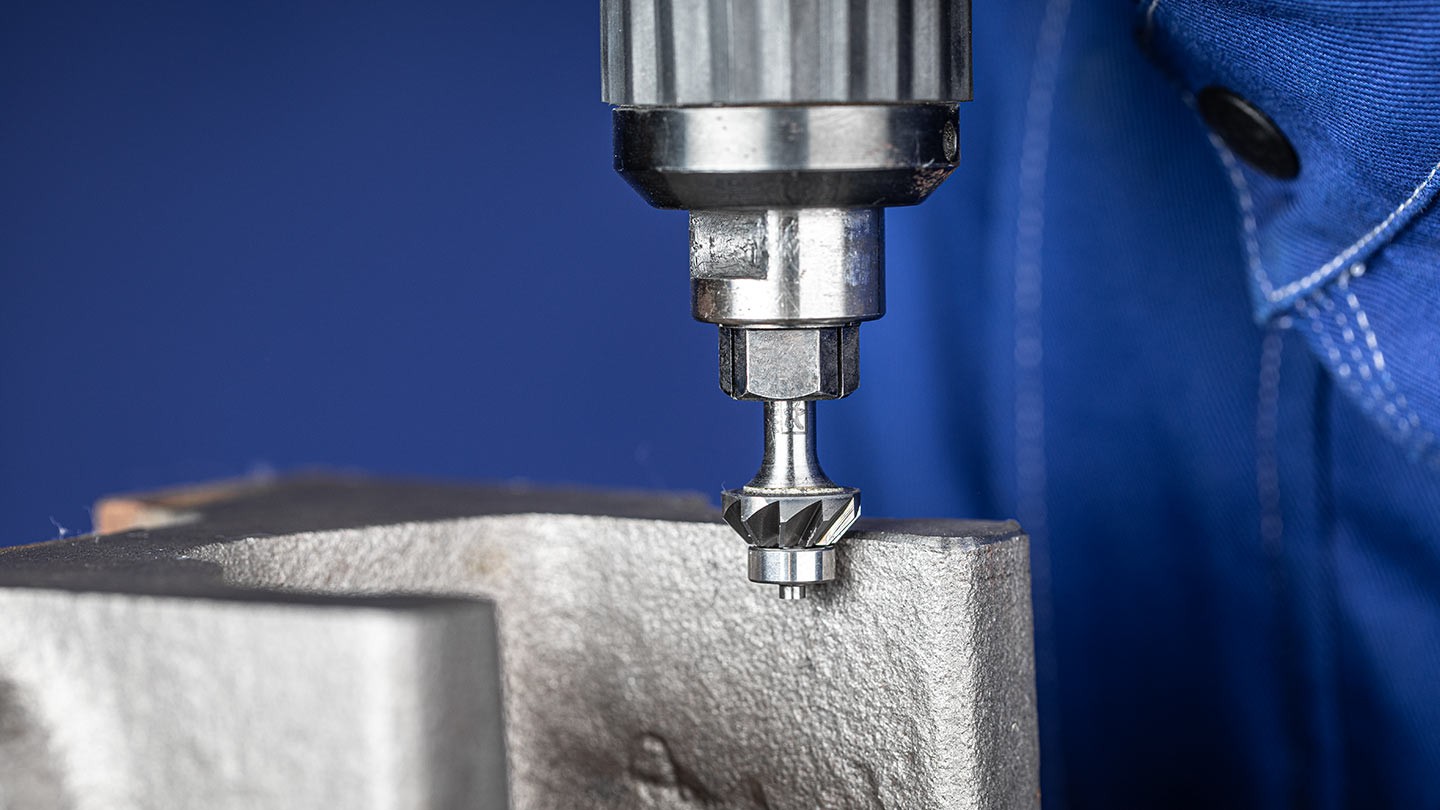
Tungsten carbide burrs with the EDGE cut have been especially developed for defined work on edges. Their special design allows the burr to run directly along the edges without damaging the workpiece.
Exact edge shapes can therefore be created in a single step – with either defined chamfers of 30° or 45°, or to a defined radius of 3.0 mm. Among other things, rounding edges is a precautionary measure for anti-corrosion protection according to ISO 12944-3, ISO 8501-3, SOLAS XII/6.3 (Ref. T4/3.01 MSC. 1/Circ. 1198).
What burr forms are suitable for flexible work on edges?
The following burr forms are available for flexible work on edges:
Conical counterbore shape
The conical counterbore burrs in accordance with DIN 8032 with cut in line with DIN 8033 are suitable for flexible counterboring and chamfering. PFERD TOOLS offers the burrs in the versions KSJ (60°) and KSK (90°).
In the double-ended version, the burrs are cut and usable on both sides.
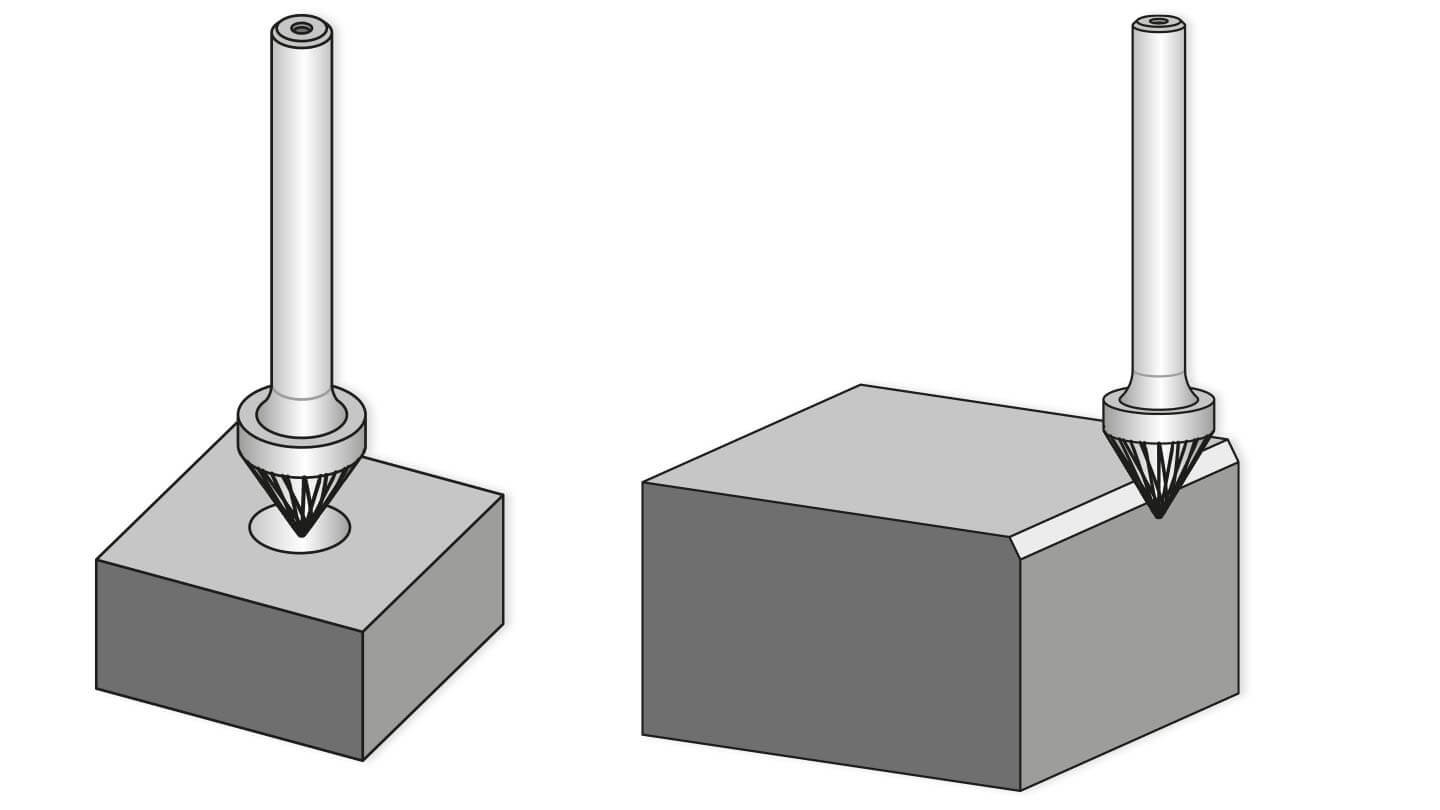
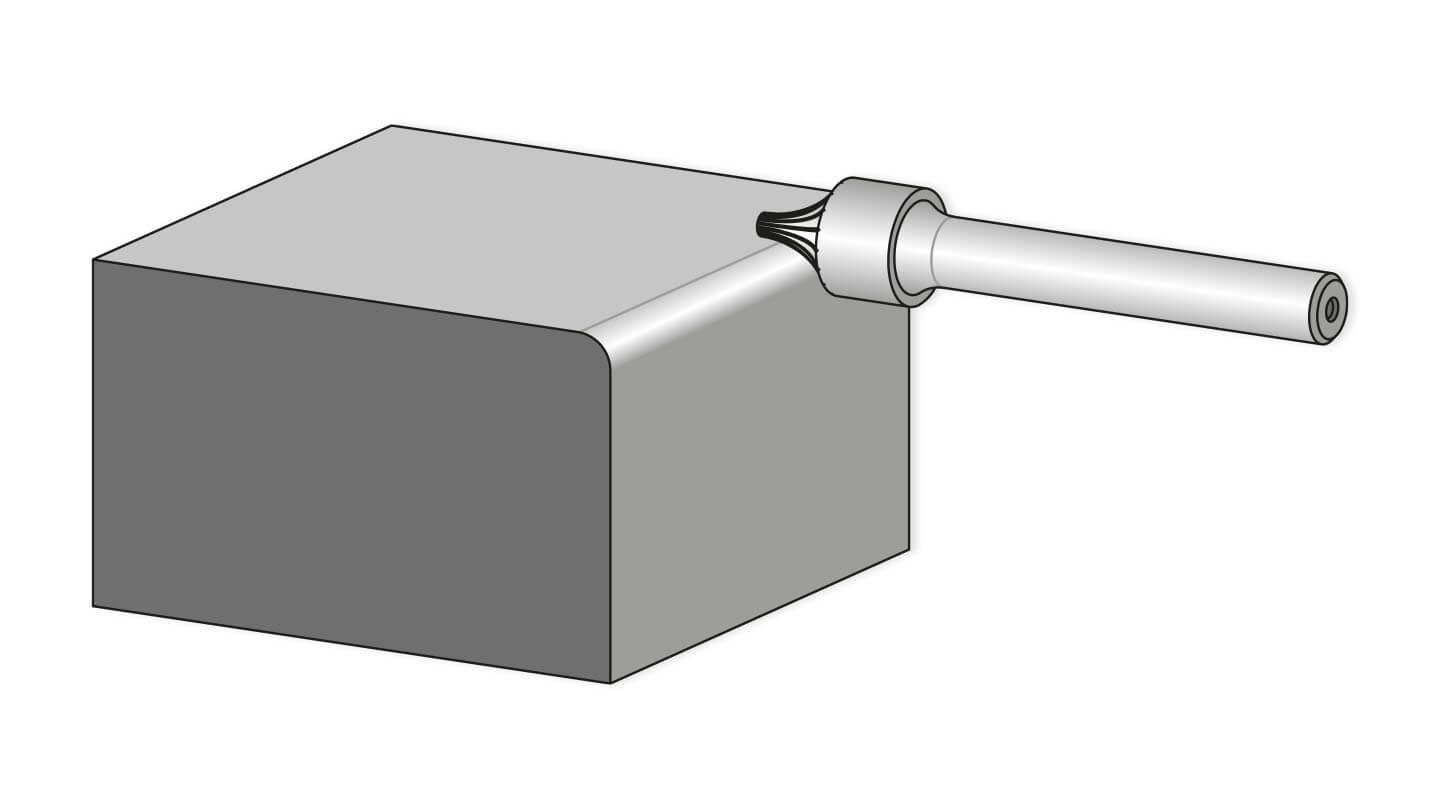
Concave radius burrs
Concave radius burrs are characterized by their concave end shape. They are cut according to DIN 8033 and are designed for the production and processing of outer radii and rounded edges. The burrs cannot be resharpened.
Radius burrs
Radius burrs with a concave shape and special cut are used in the production and processing of outer radii. They are available in two versions: cylindrical with triple concave contour; or with concave shape, tapered towards the shank. The burrs cannot be resharpened
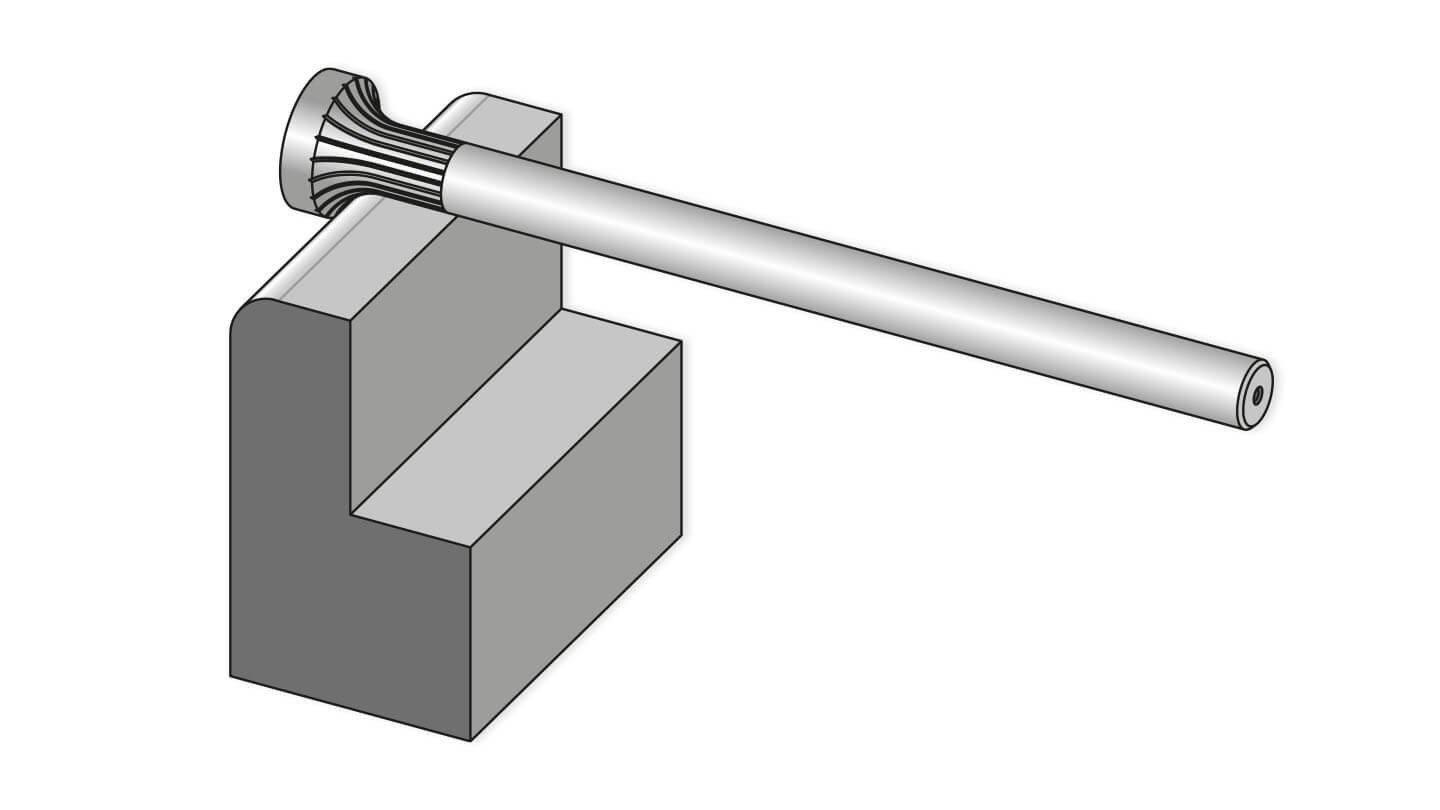
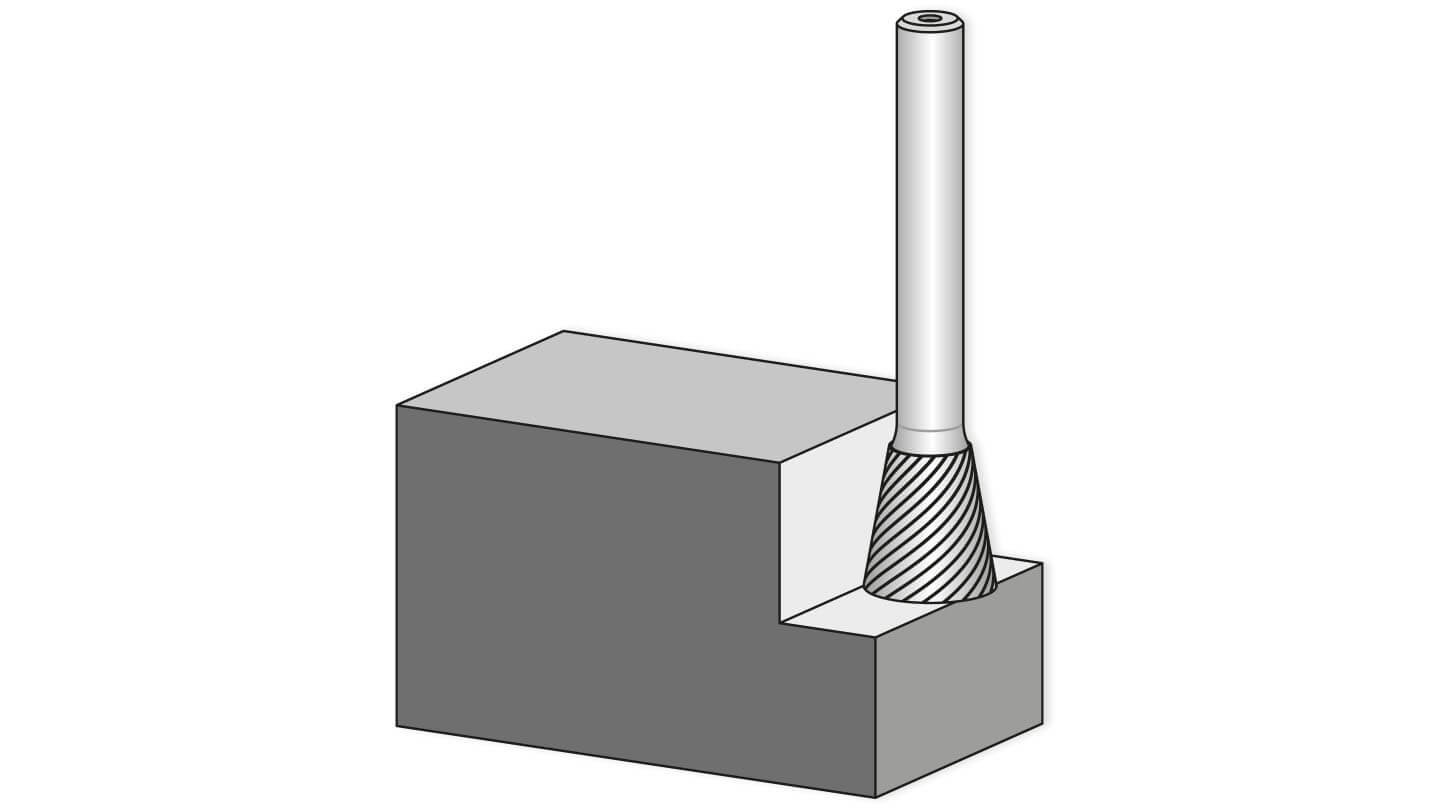
Inverted cones
Inverted cones are cone-shaped burrs tapered towards the shank according to DIN 8032 with cut conforming to DIN 8033. They are used for work on hard-to-reach, reverse-side edges.
PFERD TOOLS offers inverted cones in the versions WKN and WKNS. WKN is the version without end cut and WKNS the version with end cut
What cut is suitable for flexible work on edges?
PFERD TOOLS recommends tungsten carbide burrs with the cuts 3, 3 PLUS, 5 as well as burrs with special cut (SP) for flexible work on edges. Thanks to their special shapes, these burrs create very precise chamfers and radii.
The burrs can be guided as desired, and can also be used flexibly on hard-to-reach areas.
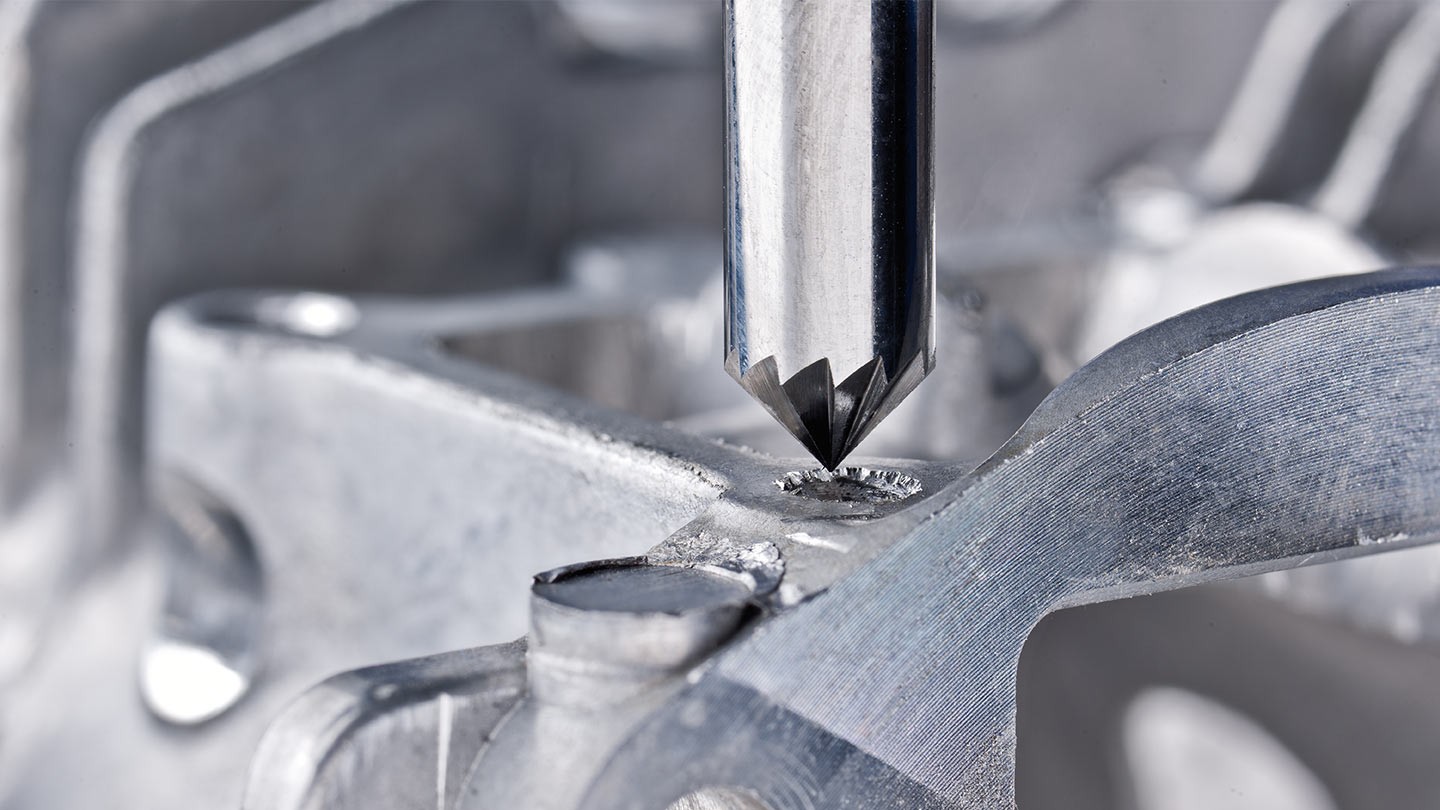
EDGE Cutting System
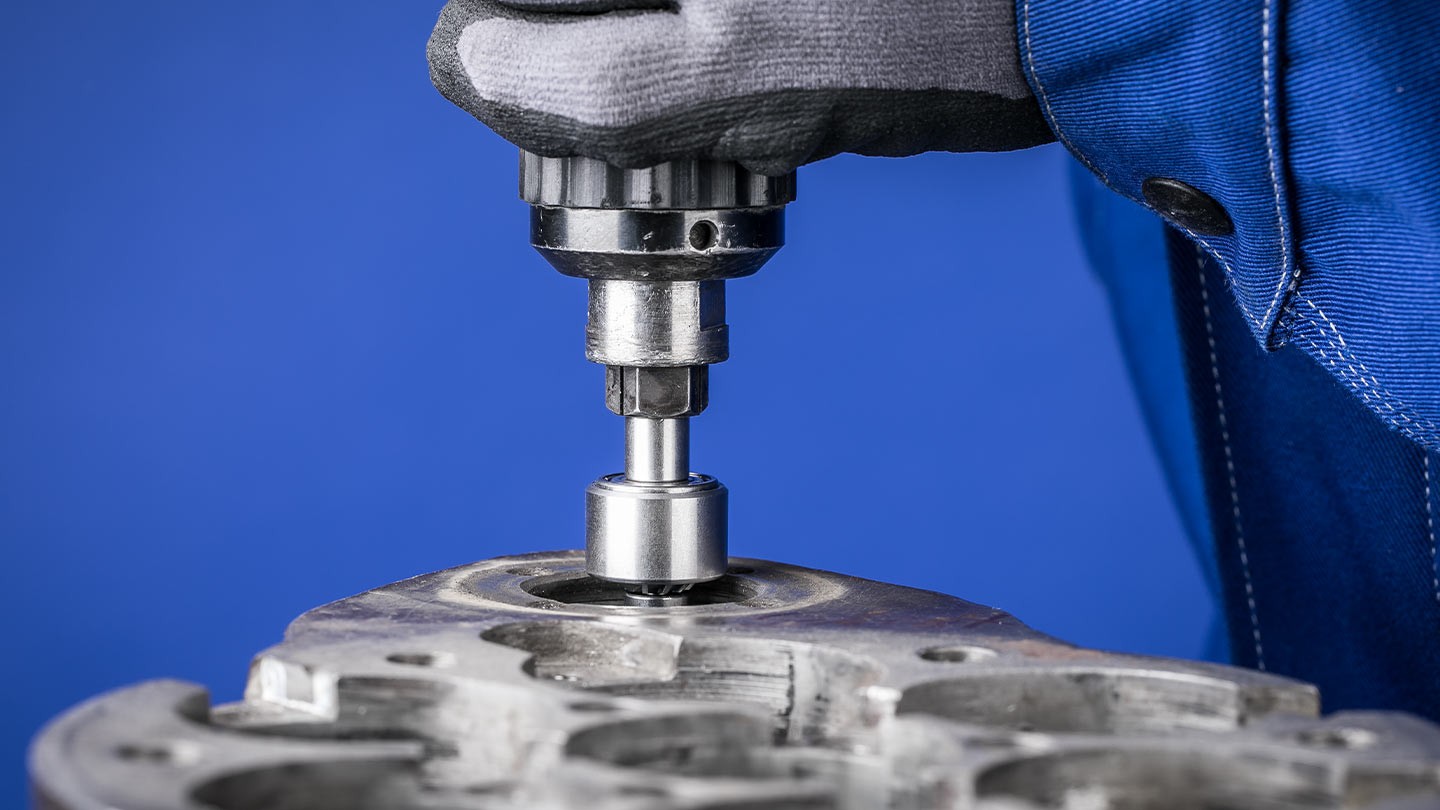
The EDGE Cutting System consists of burrs with the EDGE cut and a special guide sleeve.
The system can be used on any commercially available drive to ensure optimal guidance during light deburring work.
EDGE Cutting System burrs can be reordered and replaced if required.