Mounted flap wheels: small master grinders
Mounted flap wheels from PFERD TOOLS are excellent tools for close work at edges and in angles. The flaps consist of abrasives on a base and are extremely flexible. As new, aggressive abrasives are continuously exposed, the stock removal rate remains consistently high – throughout the entire tool life.
What is the structure of mounted flap wheels?
On mounted flap wheels, the flaps made of abrasive on a flexible base are arranged radially around the tool axis to create a sunburst.
Their flexibility enables them to adapt perfectly to the contours of the workpiece. The abrasive grain is embedded in the sturdy, flexible cloth backing material by means of a resinoid bond.
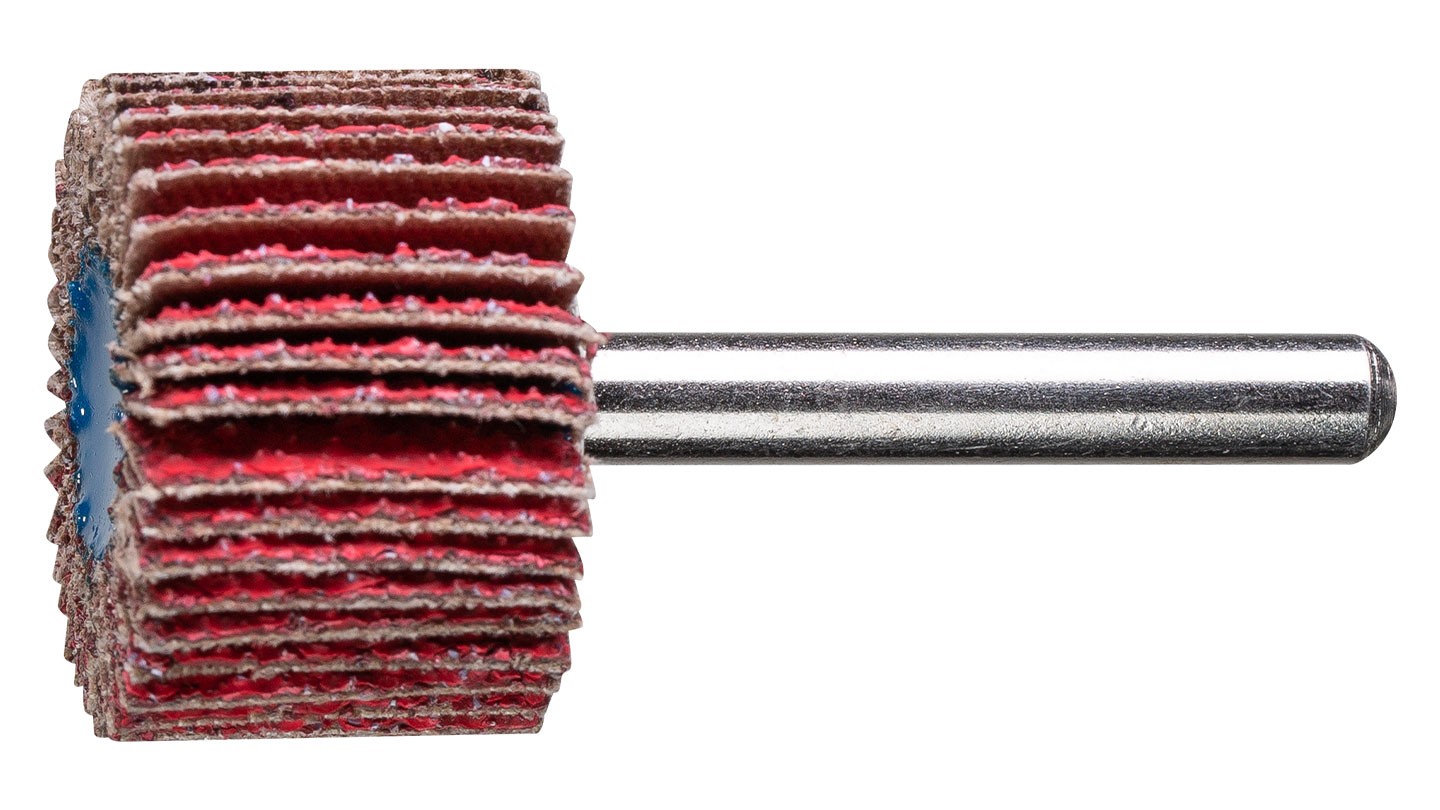
What types of mounted flap wheels are there?
The following mounted flap wheel versions are available in the PFERD TOOLS range:
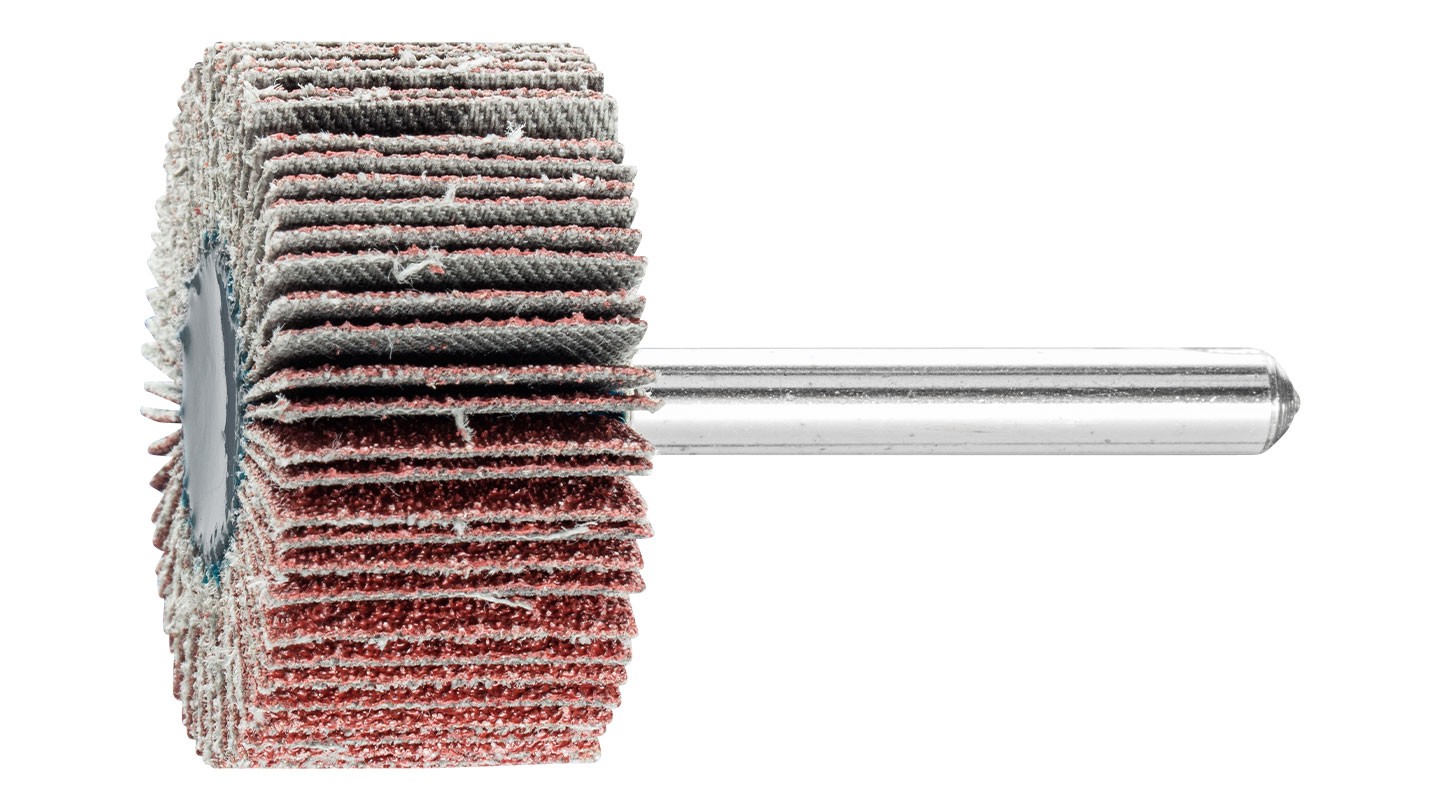
Zirconia alumina Z-COOL
For coarse grinding work with a high stock removal rate and cool grinding.
Active grinding additives in the coating substantially improve the stock removal rate, prevent clogging and result in cooler grinding.
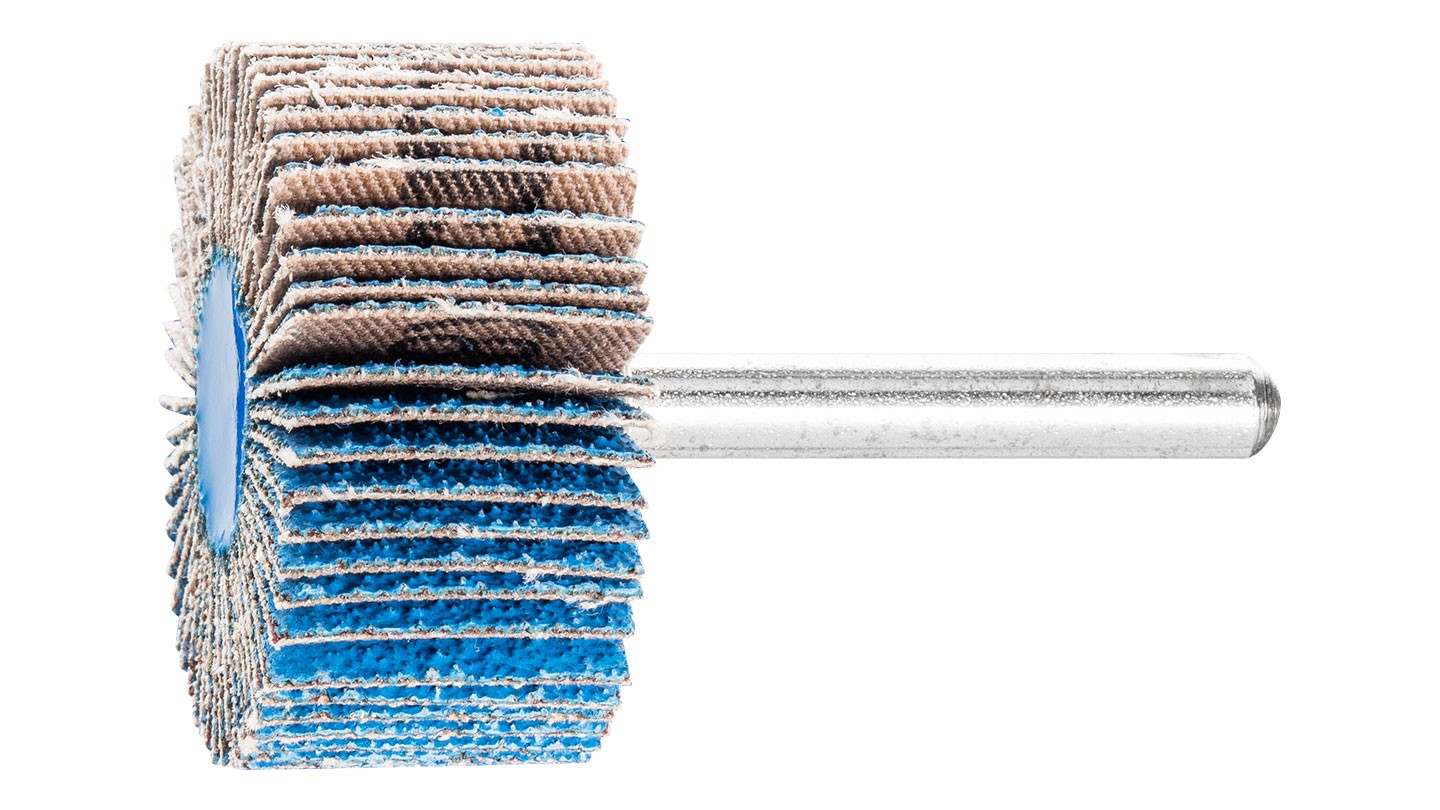
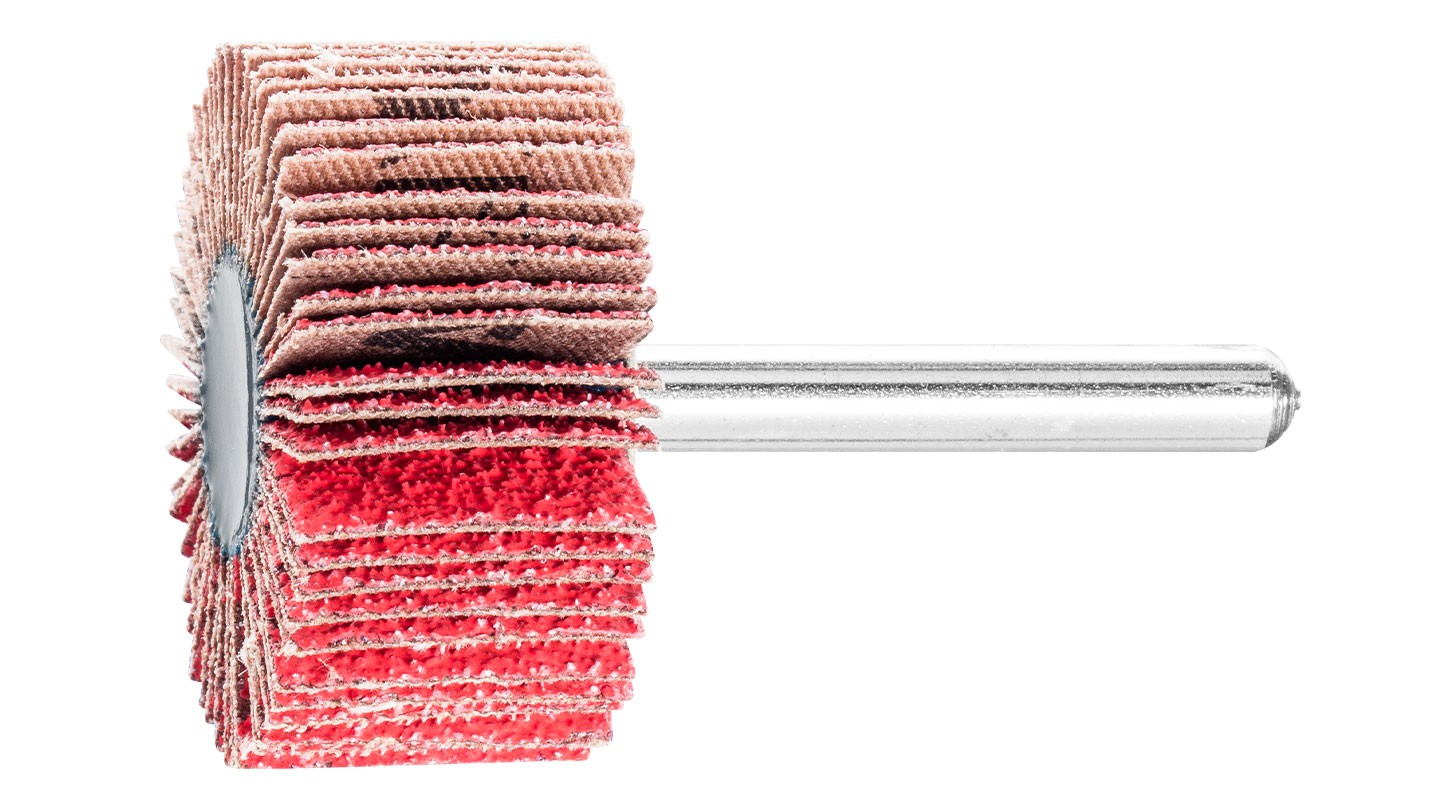
Ceramic oxide grain CO-COOL
For aggressive grinding with maximum stock removal rate on hard materials with poor thermal conduction.
Consistently high performance due to self-sharpening ceramic oxide grain.
Active grinding additives in the coating substantially improve the stock removal rate, prevent clogging and result in cooler grinding.
Silicon carbide SiC
For general grinding work on components made from aluminium, copper, bronze, titanium and fibre-reinforced plastics.
Particularly recommended for use on titanium alloys.
Ideally suited for use in the aircraft industry, particularly when SiC is the only abrasive approved for use on engine components, for example.

Which advantages do mounted flap wheels offer?
What is it important to know when working with mounted flap wheels?
You should observe the following recommendations for use in order to successfully use mounted flap wheels:
Tool wear and thermal load
Reducing the contact pressure and the peripheral speed and adding grinding oil diminishes tool wear and thermal load on the workpiece.
Stock removal rate
To increase the stock removal rate, it is advisable to use a coarser grit instead of increasing the contact pressure. This will prevent unnecessary tool wear and thermal load on the workpiece.
Surface roughness
The increase in cutting speed leads to a slightly finer surface quality. Increasing the contact pressure makes the surface slightly coarser. The softer the material that is being worked on, the coarser the surface (when using the same grit size).